Comprehensive Container Welding Evaluation for Industrial Safety And Security and Regulatory Compliance
Making certain commercial safety and security and regulative conformity within the world of container welding evaluations is an important element of preserving operational stability and mitigating prospective risks. The thorough exam of weld quality, product density, and total storage tank problem is extremely important in protecting against environmental risks and structural failings. By diving right into the complexities of thorough container welding evaluations, a deeper understanding arises of the diverse techniques employed to support sector criteria and promote security protocols.
Relevance of Tank Welding Examinations
Performing periodic and detailed container welding examinations is crucial in making certain the architectural honesty, safety criteria, and regulatory conformity of industrial storage tanks. These evaluations play an important function in identifying any kind of prospective issues or weak points in the bonded joints that can endanger the total stability of the tank. By finding these concerns early, firms can take proactive steps to resolve them quickly, consequently avoiding pricey repair work, environmental contamination, or, in the worst-case circumstance, tragic failures.
Routine container welding evaluations likewise aid companies adhere to market guidelines and requirements established forth by authorities such as the American Petroleum Institute (API) or Occupational Security and Health Management (OSHA) Failure to fulfill these needs can cause fines, legal effects, or perhaps the suspension of procedures. Tank Welding Inspection Service. Consequently, buying thorough storage tank welding assessments not just safeguards the wellness of personnel and the surrounding setting but additionally protects the company's reputation and profits in the long run
Trick Elements of Weld High Quality Analysis
Making certain the top quality of welds involves a careful assessment of key parts that contribute to the architectural stability and reliability of industrial tanks. One vital aspect of weld quality assessment is the exam of weld penetration. By thoroughly examining these crucial elements, assessors can aid ensure that bonded joints satisfy the necessary standards for security and regulatory compliance in commercial storage tank building.
Material Density Examination Strategies
In the context of weld top quality analysis, an important aspect to think about is the application of material thickness assessment techniques. Accurate measurement of product density is important in making certain the structural stability and safety and security of bonded tanks. Different non-destructive testing (NDT) techniques are utilized for analyzing product thickness, consisting of ultrasonic screening, radiographic screening, and magnetic fragment inspection. Ultrasonic screening entails the usage of high-frequency acoustic waves to identify product density by gauging the moment considered the acoustic waves to take a trip via the material and reflect back. Radiographic screening uses X-rays or gamma rays to generate pictures revealing worldly thickness. Magnetic particle inspection works for detecting surface area and near-surface problems that might impact product thickness. These techniques not only assist in examining the density of products however also aid in identifying any type of potential defects or stoppages that might endanger the weld high quality and overall honesty of the tank framework. By using these material density assessment strategies, industries can guarantee conformity with safety requirements and guidelines, therefore improving general operational safety and reliability.
Container Problem Examination Methods
An important facet in preserving the integrity and security of bonded tanks is the comprehensive examination of tank conditions with trusted evaluation methods. Container problem evaluation methods play a critical role in ensuring the structural stability and functional effectiveness of commercial storage tanks. Aesthetic evaluation is a primary approach used to assess the exterior problem of tanks, trying to find signs of deterioration, leakages, or physical damages. In addition, non-destructive testing techniques such as ultrasonic testing and radiographic testing are used to identify internal problems, weld problems, and product destruction that may endanger the container's efficiency. view publisher site Tank Welding Inspection Service. Moreover, magnetic fragment inspection can recognize surface area fractures and issues that are not noticeable to the nude eye. These assessment methods offer useful insights right into the total health and wellness of the tank, enabling early discovery of potential problems and facilitating prompt upkeep or repairs to make sure conformity with safety and security regulations and market requirements. Routine assessments using these methods are essential for stopping devastating failures and ensuring the lasting reliability of welded containers.
Benefits of Normal Inspection Practices
Regular inspection practices not only protect versus possible concerns spotted throughout storage tank problem evaluation methods yet also function as positive actions in promoting the structural stability and operational performance of bonded tanks. By performing normal examinations, industrial centers can identify any kind of indicators of corrosion, cracks, leakages, or various other defects in the tank welds quickly. This very early discovery allows prompt fixings or upkeep interventions, stopping little concerns from rising right into larger, more costly issues that could endanger safety or bring about regulatory non-compliance.
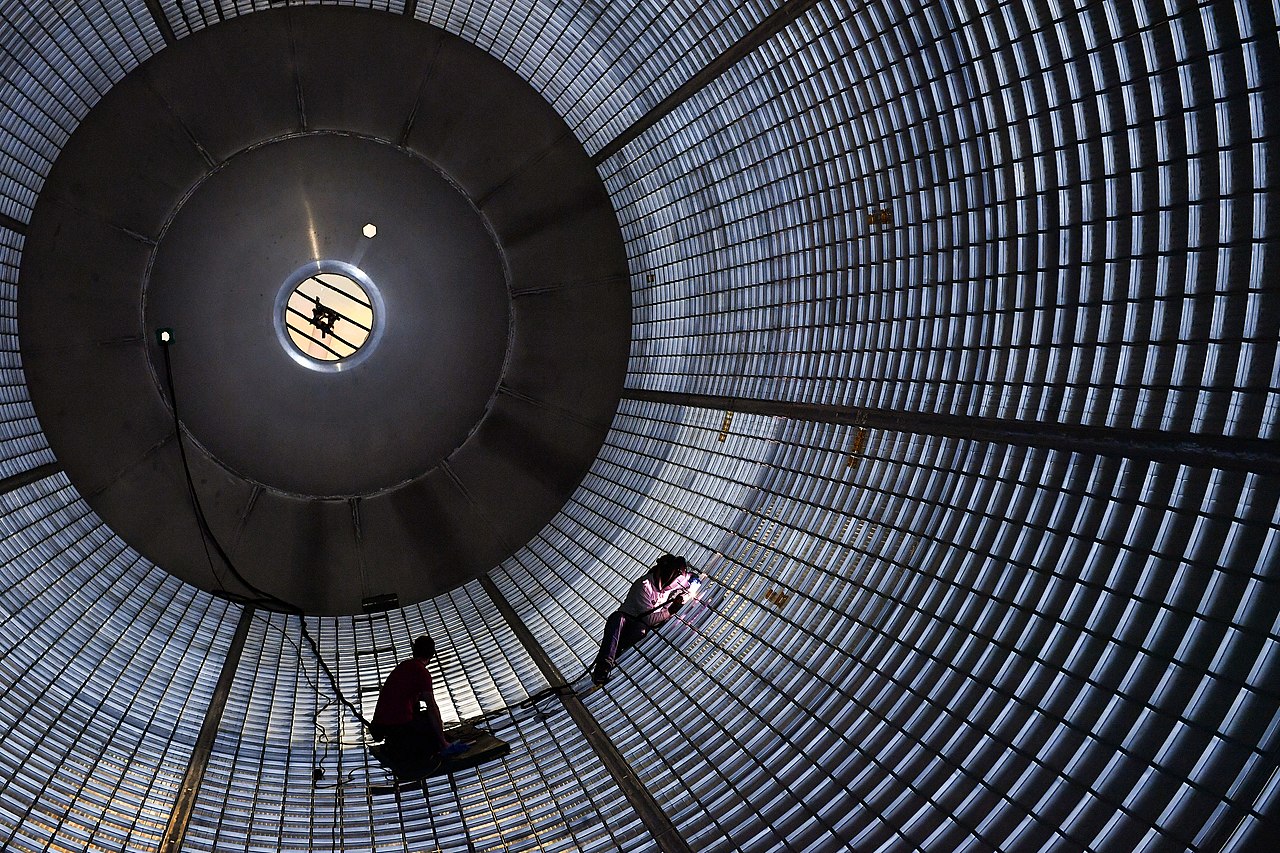
Final Thought

In verdict, extensive container welding assessments are crucial for guaranteeing commercial safety my website and regulative compliance. By performing regular evaluations and evaluations of weld top quality, product density, and container condition, companies can determine potential dangers and stop costly accidents. Implementing a proactive approach to examination practices can aid keep the architectural stability of tanks, protect the atmosphere, and guarantee the safety of workers and the surrounding area.
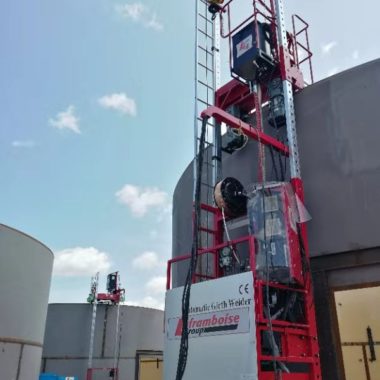